How Much Does It Cost To Make A Product?
How Much Does It Cost To Make A Product?
Are you struggling with calculating a definite number before developing your product? A market analysis, cost-effective raw materials and a quality product is what it takes to take over your niche business. How can a buyer effectively employ price analysis to their product to arrive at the stated prices? Let's run through the hypothetical process to determine your product's ultimate cost.
For example, in order to determine the price of product "X" using price analysis, the following procedures could be used:
- To gain a notion of the market and publicized prices, conduct a general internet search on the item using multiple shopping sites and search engines.
- For a suggested retail price, contact the manufacturer directly
- Obtain pricing quotes on the same item from competing brands or manufacturers and use price indices.
- To gain a better understanding of what others have paid for the identical item, we recommend getting guidance from industry peers.
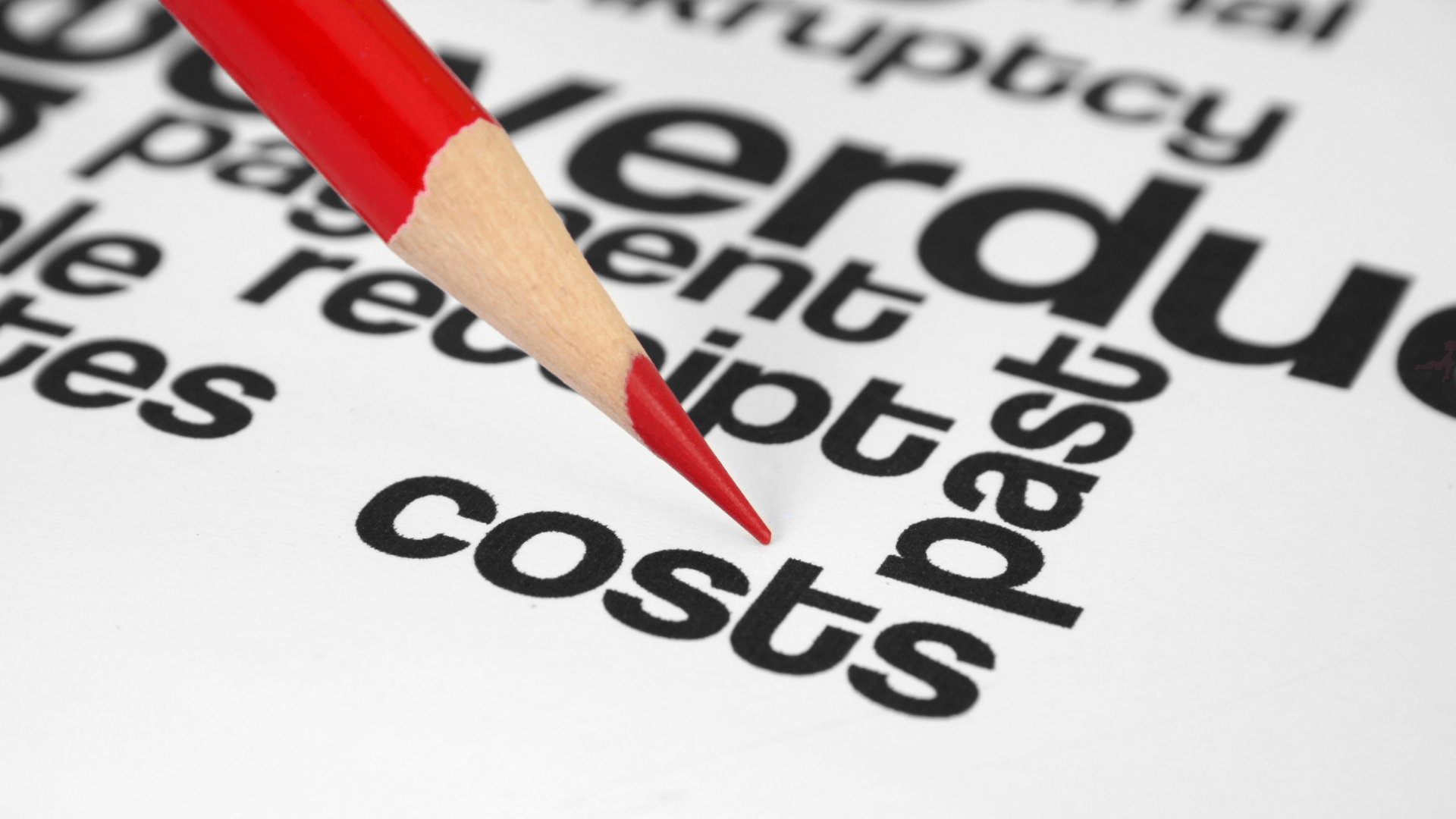
Using the above strategies is a sure-shot way where you can determine what your product is truly worth.
There are many ways to think about product development costs, but one number captures it all—the total costs of bringing a new product to market. That number will be different for every organization, but the ultimate goal is to lower it. Reducing the overall cost can allow an organization to bring products to market more quickly and less financial risk.
A well-planned process might start with generating ideas, then defining features or functions in detail, then prototyping or proof-of-concept testing at various stages in the project life cycle. But when you’re discussing costs with your business unit managers, it’s essential to define them carefully at the beginning, so you know what you’re managing.
During the product design production, a smart strategy would be calculating the manufacturing cost along with components/raw materials used to produce the prototypes. Calculate the cost to make the product design of the prototype.
Fixed Costs
Once you’ve established a budget for your project, fixed costs are often one of the first things to drive up your total cost. This can happen when new technologies, market data, or software tools become available during the process. While a more experienced team may be able to work faster and get better results from its existing resources, decisions about which new tools to use aren’t always easy because of potential risks if they don’t work out as planned.
Variable Costs
This category includes costs that could potentially go up or down as a project progresses, such as engineering time and factory labor for parts manufacturing. In general, the cost of development work falls into this category, along with direct materials used to manufacture a product and acquire it from suppliers. But what you’re really thinking about when you think about variable costs are these two questions: Is this something we can begin doing now? And is there a risk that if we wait until later in the project to do it, the additional effort will increase the cost by an unacceptable amount? The more uncertain your answer to those questions, the greater your risk of going over budget because of variable costs.
Fixed Overhead
This one is important to consider in almost any discussion about product costs because it represents unavoidable costs that don’t go away as a project progresses, such as management and support staff salaries like rent and utilities.
Calculate the cost of raw materials, production of minimum order, the price for a product design, production of the prototype, a rough estimate on profits and sales, pricing and packaging, how much to spend on engineering, different prototypes, the launch of the product, testing pricing, etc.
Product Development
It is the central stage in any manufacturing business. This is where you plan and specify what will be made and determine how it's going to be made. It includes such fields as design, engineering, and testing.
Every manufacturer looks at the design process differently because of its history, culture, corporate structures, and technology. Many companies outsource this production phase because they don't have the facilities or personnel needed to complete it themselves (OEMs - original equipment manufacturers).
The manufacturer must design different ideas and use different raw materials to create a custom tool for their own company. This will help in prototyping future custom product designs. Testing the packaging stage is essential to estimate profit and sales generated from that particulate prototype/idea.
The steps involved in developing a product:
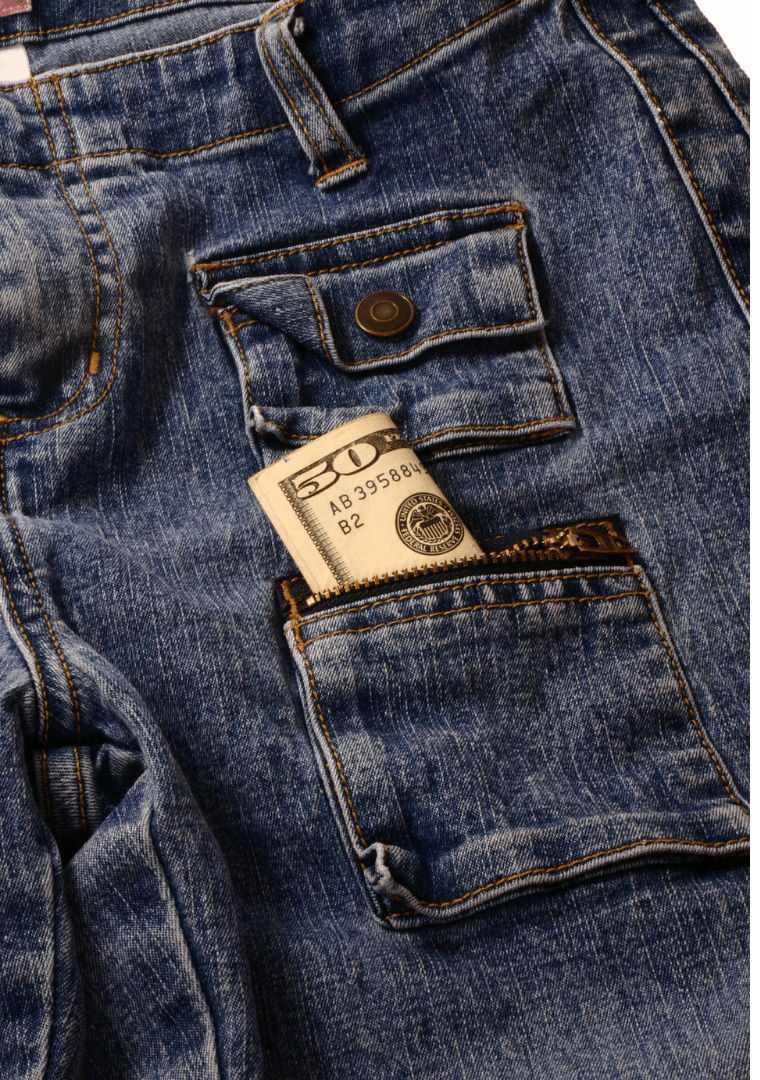
Manufacturing Cost
The next step for producing a product is manufacturing. Manufacturing cost in this phase includes material. Your product will be tested before it is sold. You will need testing and assembly fixtures to design custom prototypes.
By calculating manufacturing cost, the manufacturer can know what portion of cash, at what point in time, is required to produce a product. The first item to add is a factory's margin. For example, tooling can help to develop an effective strategy used to calculate the factory's margin.
The first stage/step is calculation is a material estimation, where you need to estimate basic parameters like quantity, flow rates, efficiency, and more. With these parameter estimations, you will be able to establish material usage projections. Material costs are based on unit prices that different suppliers or unknown manufacturers have filtered out. Various reasons contribute towards fluctuation in material prices, usually linked with inflation and currency exchange rates. These fluctuations may result in an increase or decrease in overall manufacturing costs. Let a team of professionals calculate the entire cost for manufacturing various products. It is a smart move, and it will give you an estimate of how much money is required to get the project done. This will also let you know for how long your product will keep giving you profits and when it will stop doing so.
Book an appointment with our team of highly skilled experts who have years of experience to help you get accurate answers that you might want. Ask any questions from our team of pros, and we will provide you with the answers you've been looking for. Let our team of experts handle the job for your business.
Manufacturing labor cost is one of the significant components of manufacturing costs. This cost depends on various factors like level of worker knowledge, skill, and experience. Factories with experienced workers can handle more workload than a factory staffed by inexperienced workers will require less time to complete the same task. Factory production/manufacture of high-quality products with great packaging comes at a high cost. The assembly of every prototype and tooling high-quality packaging has a great price. But the good news is that if you have control over your production cost, then the prototype production can be attained at a low cost.
The next element in manufacturing cost calculation is overhead expenses, including energy usage (electricity, water, fuel), insurance fees for machinery, repair & maintenance services (equipment related), and other items that affect production costs like environmental regulations compliance.
As per definition, you will need to add up all the material costs together then match it against the estimated number of units produced or an actual number of units produced within a specific timeframe. The difference between these two numbers will show you the amount of material wasted or consumed. Labor cost is calculated by dividing total hours by the number of units completed within a specific timeframe.
Finally, overhead (energy-related) expenses are added to the total manufacturing costs. By adding material and labor costs together, you will get your final cost per unit. We recommend that you do your research about manufacturing costs so you can put an affordable price for your product. The main goal is to provide a product to your beneficial customers. A good product will go a long way in making a lot of profits for your company. To achieve complete success in manufacturing, you must first calculate all the cost to manufacture an amount of product. This will give you a rough estimate and help you in making future decisions more clearly.
A material estimation has to be done very accurately. Otherwise, it may lead to overproduction or underproduction, which affects overall profits severely. Similarly, if there is no proper estimation of human resources involved in the production process, then it can also affect entire productivity immensely as well as profitability. When these two factors are not appropriately estimated, they result in various problems like increased lead time for the product, decreased efficiency linked with product manufacturing, and high manufacturing cost, which drastically reduces profitability. Hence, it is essential to estimate these factors with proper care to avoid all problems at later stages of the production process. By following accurate estimation techniques for the material involved in the product, manufacturing will significantly boost the company's profitability while also increasing overall productivity considerably.
An effective prototype manufacture strategy with low risk can be attained at a low price. For example, you can manufacture a prototype only when you need it. It is crucial to calculate manufacturing costs before you start to manufacture your product. A brought estimate will help in setting that amount aside.
It is recommended to conduct thorough research before establishing a final price tag or quotation for your products. The manufacturers should know what their competitors are charging/selling their products for and then select a competitive price range rather than providing prices much lower than what other companies are offering.
There is no clear answer; a physical product is one type of cost. At the same time, tech/media/social is another costing model. A service yet another model. Or contact us at
www.cooksoutsourcingnetwork.com.
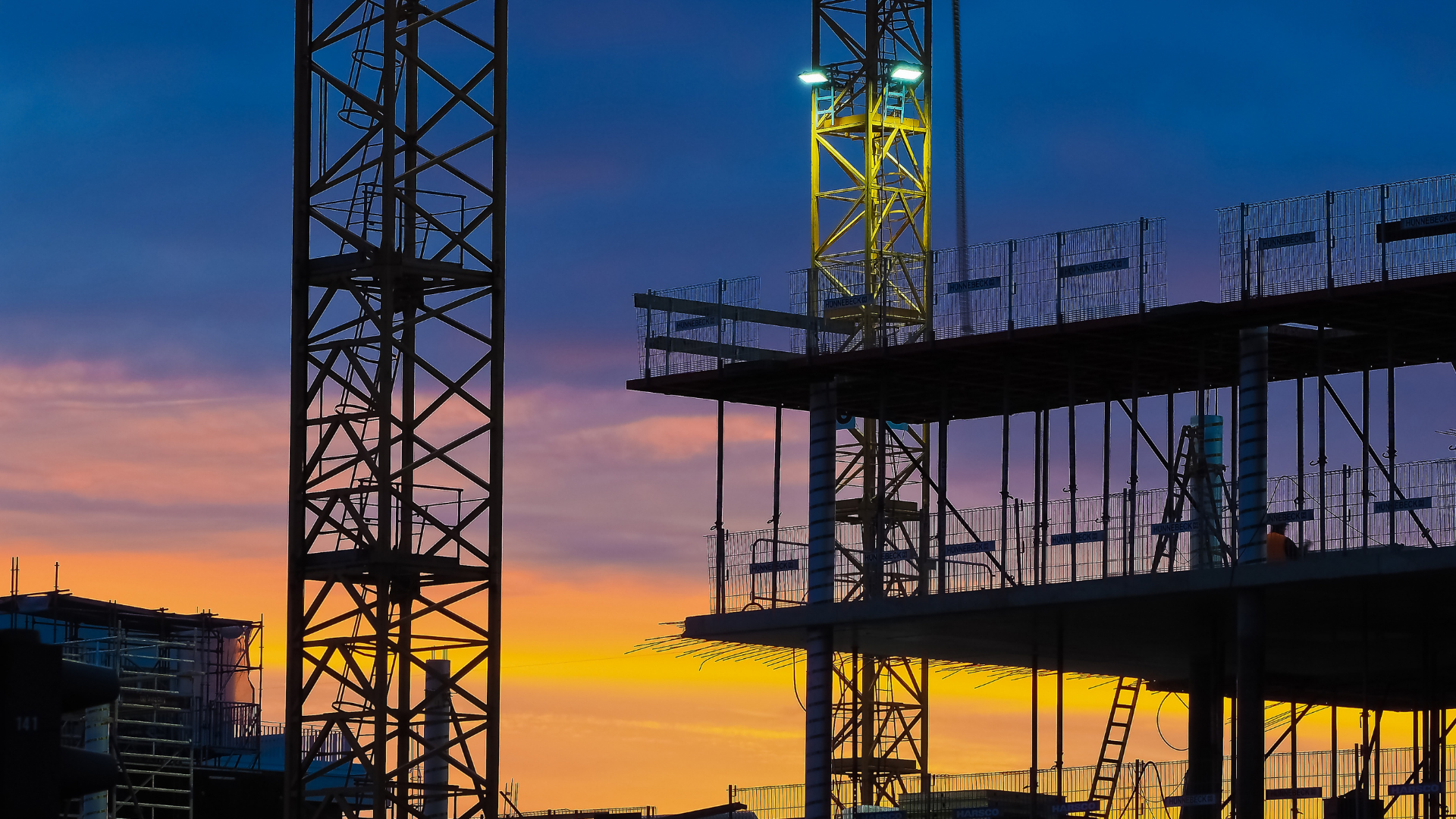
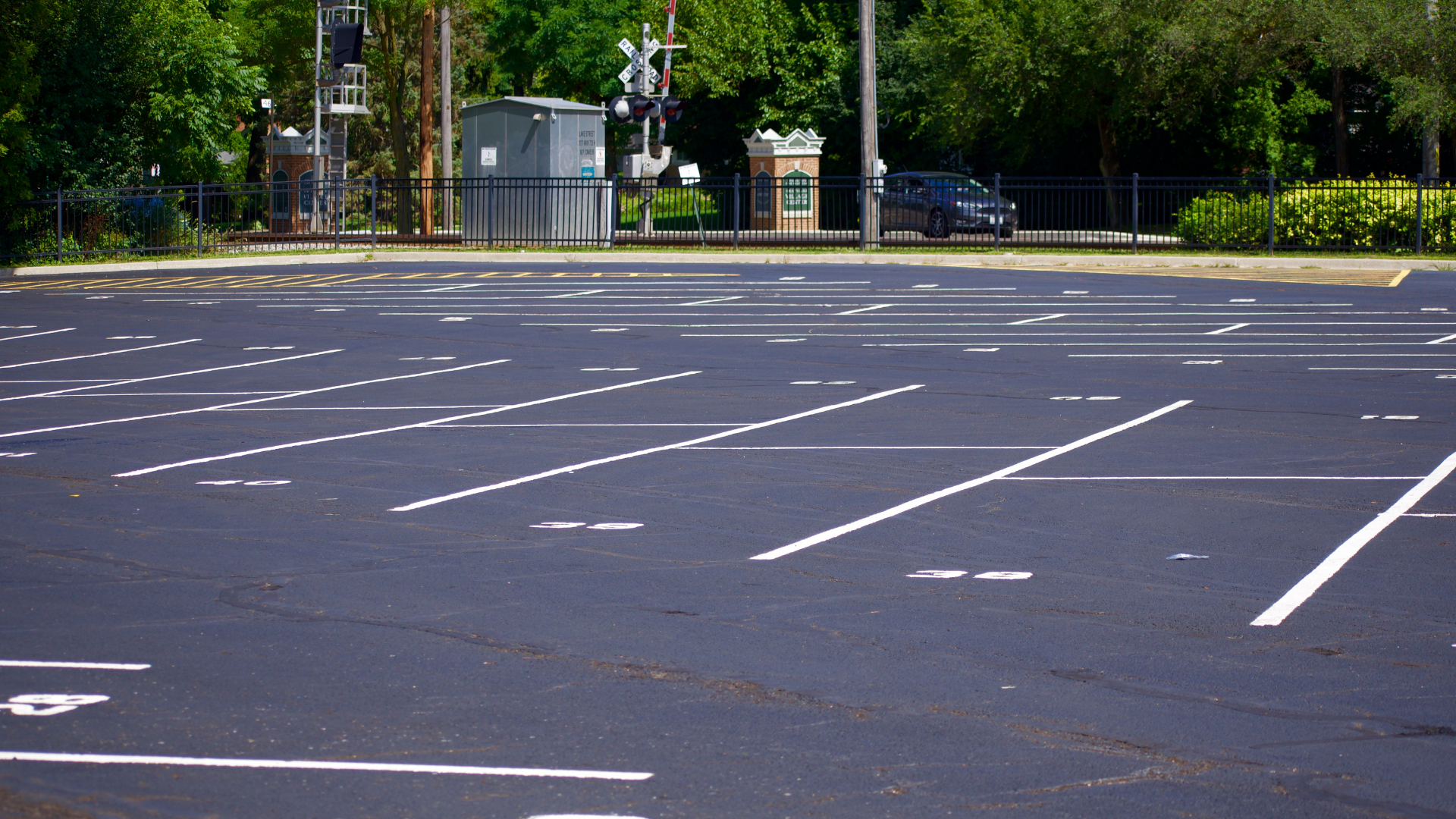